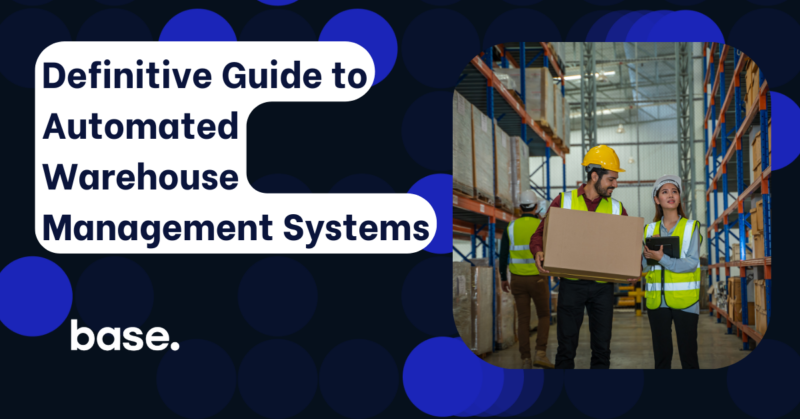
Warehouse management is the first efficiency checkpoint. It’s where the majority of your manual efforts, resources and time are concentrated. And yet, it’s also the place that sees a snowball effect when things go wrong, which is why several sellers are migrating to an automated warehouse management system ,a.k.a a WMS. As eCommerce and its spinoffs such as Q-Commerce, m and v-Commerce experience an uptick, India is expected to be one of the top 6 users worldwide who will rely on WMS systems by 2026.
When managed through WMS, you can ensure that your inventory is always at optimal levels and stock replenishment is adjusted to demand planning. And both contribute to having inventory at the right location in-time, which is the means to achieving the end goal of frictionless customer experiences.
Let’s talk about where WMS solution is most useful and take you through all the steps within the Base Warehouse Management System Module to underline its purpose within the broader context of supply chain management.
What are Warehouse Management systems?
Different activities impact inventory levels, including returns and separating them by quality and reusability. A Warehouse Management System (WMS) is a technology platform that automates warehousing operations.
It is designed to help everyone in the supply chain- be it manufacturers, sellers, retailers and distributors to keep an eye on inventory movements. WMS software takes care of warehouse-level stock availability, storage, order processing and order tracking throughout so that delivery status reflects consistently to the seller and customer alike. Even if there’s a disparity, there’s added accountability that makes it easier to nip financial leaks and inefficiencies.
Warehouse management entails all activities of inventory management, order fulfillment, storage and shipping. It comprises:
- Inventory Control: Tracking inventory through automated and physical counts to ensure inventory adequacy without over or under-stocking.
- Order Fulfillment: Facilitating the shortest and accurate pick-to-ship processes.
- Space optimization: Making use of the existing space to reduce search movements and maximize utilization.
- Logistics Coordination: Managing inbound, outbound and reverse logistics to ensure smooth movement of goods.
The Importance of Warehouse Management Systems
A WMS enhances decision-making by giving sellers insights that enable them to weigh and boost the profitability of their operations. Within the system, there’s a centralized dashboard to accommodate omnichannel touchpoints that connect your store to customers, whether you operate on a D2C, wholesale(B2B), or dropshipping model. Through a WMS, you can
- Add orders and create lists for products and orders separately, such that a debit on the product side is recorded as a credit on the order side. This continues until your stock level reaches 0, and allows you to activate replenishment triggers to suppliers. Timing your transaction closer to demand not only prevents over or under-stocking but also reshuffles existing products to starving warehouses.
- Reduce order fulfillment errors by removing the manual intervention linked with putaway, item retrieval, picking and packing.
- Estimate order quantities and ready your warehouse team to receive, inspect and approve or question item quality coming in from different suppliers.
- Expedite order processing so that it reaches your customers on or even ahead of time.
- Manages inflow of returns and marks their return delivery, highlighting quantity discrepancies so that returns that are missing or lost can be taken up with the respective courier partner.
- Upscale your business in line with a larger inventory, more customers, order volume and gross merchandise value. The system can adapt to the change as you expand and add more sales channels.
A robust WMS is more than just a tool to manage your eCommerce warehouse or distribution center. It’s an essential system that helps improve service to your customers, providing you with a competitive edge in the highly competitive marketplace.
Different WMS Types
-
Standalone WMS
An independent or standalone WMS is best suited for specific warehouse operations and for businesses operating in a certain niche and growth scale. It is the most cost-effective option unless you require it to integrate with ERP or accounting platforms, in which case additional investment will be required.
-
Integrated WMS
An integrated WMS is fused into an existing ecosystem of accounting and logistics software, each of which generate different reports that get consolidated and made visible as a single source of truth. It is this unification that saves time and drives efficiency. Integrated WMS is an upgrade from the standalone WMS as it is more free-form and works with non-WMS systems.
-
Cloud-based WMS
Cloud-based WMS systems are SaaS-based, and are gaining rapid popularity for their customization, security and flexibility. The system is hosted on the cloud and accessed on the internet. A seller can monitor warehouse activities through App or browser. They can instantly verify particulars, store information, retrieve reports and scan items on the go which reduces infrastructure costs.
-
On-site WMS
An onsite WMS is installed directly on the company’s servers and closely monitored by the IT team. It requires a sizable investment from the business to purchase hardware such as RFID and barcode scanners which is great for security.
WMS on Base Explained
The Base WMS runs on a number of Automatic Actions designed to simplify and quicken warehousing operations. The first step is to add a group of actions under a function, i.e. “warehouse” before further automatic actions.
Every action has an event and trigger, and the default pre-programmed events for warehouse-based automatic actions are
- Order not fulfilled/ Stock shortage
- Reservation over Stock
In the former, the WMS works correctly after setting the negative stock field to “Block Negative Stock”.
To do this, the user has to go into the settings under Product tab located on the left hand side of the panel and goto settings. Use the edit inventory option available under the specified catalog and set the negative stock field as “block negative stock”. This action ensures that orders will not be fulfilled after the stock hits zero.
Apart from that, the moment of order fulfilment must be other than confirmation of the order:
Under the method of purchase costs calculations, additional options will appear:
The warehouse management system can be set up:
- Basic – simple storage data, common product stock, multi-locations without exact location stock
- Advanced – tracking each piece individually, stock at given locations, batches, serial numbers.
If “Advanced” is selected, it is possible to define additional parameters for each item – Location (required), expiration date, batch or serial number. These parameters are determined upon delivery and inventory of goods. WMS units are displayed on all documents.
- Product card
On the product card in the ‘Sales and warehouse’ tab, a new ‘Pieces’ tile is visible next to the location:
When clicked, a modal will open, displaying the current product pieces in specific locations:
Each location is visible in a separate row with its own stock, allocation (=quantity reserved in the picking assistant), expiry date, batch and serial number.
One unit can be stored in multiple locations – a maximum of 12 locations can be assigned to one stock item. Using the ‘Split’ option, pieces with e.g. different expiry dates can be separated. If the product stock after splitting is not consistent with the current stock of the product, a warning message will be displayed and it will not be possible to save the changes:
Product stock can be modified so that quantities are consistent before these settings can be saved.
- Purchase order
In the purchase orders module, WMS units are visible in the items list on the delivery card:
When accepting the purchase order, the item can be split into separate items. You can assign different expiry date/serial number to each. Bear in mind that the location is locked for editing for security reasons.
- Stocktakes
When creating a stocktake, just like in purchase orders, the columns with the data of each item are visible. You’ll additionally find each unit listed as a separate item:
When scanning a code of the product which has more than one unit, an error message will be displayed indicating that more than one product with that code has been found:
- Storage documents
In the storage documents there are columns with the details of the given product item as well, just as in purchase orders and stocktakes.
The exception is the Internal Transfer document, where you need to select to which location a product item is transferred from another warehouse.
- Pick-Pack assistant
The Pick-Pack assistant shows the locations of the products according to the settings, but also the expiry dates and series:
When you click on a location, a list of locations with WMS unit data will be displayed:
Locations are assigned to the assistant according to the selected purchase cost calculation method (oldest for FEFO, newest for LEFO).
- Printout and exports
In the product export templates, there is a [WMS_UNITS] section, and tags are available:
- E-mail templates
There are two tags available in the e-mail templates for products – with the shortest and longest unit expiry date. These tags can be used as part of automatic actions for products, e.g. by assigning values in additional fields.
- Automatic actions
There are two WMS-related triggers in the automatic actions for products:
- Change in product units
- Certain number of days to expiration date
Key Takeaways
In a rapidly evolving landscape where selling experiences are constantly measured around the pillars of efficiency, speed and accuracy, a warehouse management system is a powerful must-have for daily use. It not only streamlines various aspects of your supply chain but also equips you with predictive data that helps you improve and adapt for the future.
With a 30-day free trial of the complete Base set up, live implementation and endless supportive hours to answer your burning questions, The Base system can help you upscale operations without disrupting existing processes, ensuring that your profit margin is in the green forever.