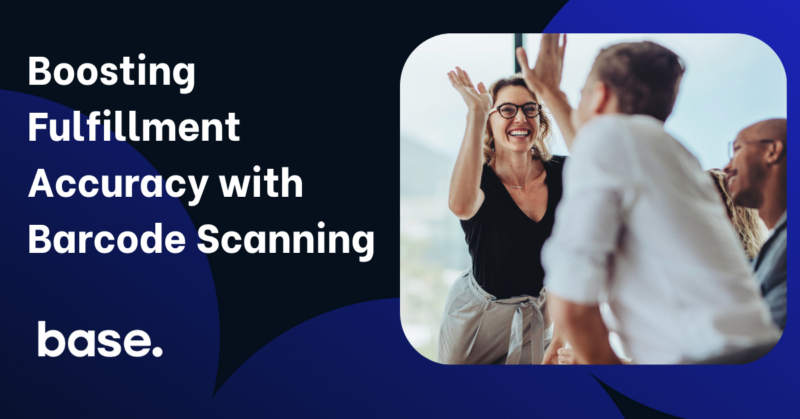
Depending on the extent of automation deployed at a warehouse, it can either be your best friend that’s making you money, or your worst enemy that will carry sunken costs and overheads that you didn’t prepare for. Speed, efficiency and accuracy is the holy trinity of warehouse management, and barcode scanners cross off all three in one strike.
The advantage to using barcode scanning is that it saves you hours of manual effort in entering data and crosschecking inventory. It instantly fetches item information based on the EAN or serial number stamped on the packaging, which allows warehouse teams to confirm they have the right item. This saves countless hours, particularly during peak demand and high sales seasons.
Accuracy and speed are also something to think about because human error, while inevitable, can distance you further from a healthy bottom line. The cost to rectify mistakes and duplicity isn’t worth it, not when you can get more done at the same time.
Let’s take a look at how the Base Barcode scanning system works, and the benefits you gain from deploying such a system at your warehouses.
What is a barcode scanner?
A barcode scanner is used to read information stored on barcodes, which is a graphical representation that looks like black and white lines. With barcode scanning, sellers can
-
Raise Order Accuracy
A barcode scanning system activates during both picking and packing processes, ensuring that the correct item moves through the chain. During picking, the picker runs the scan through an app or web, and instantly gets all relevant information necessary from the label to prevent shipping mistakes.
-
Real-Time Inventory Tracking
Did you know that barcode scanners reduce inventory errors by as much as 75%?
Real-time debits and credits to inventory levels can be confirmed and verified with a barcode scanning system. It lets you know which items are in your inventory, including the percentage of resellable returns that were returned to the shelf. These can be used to fulfill other prepaid or COD orders that come in. Thanks to the barcode, even the customer details get automatically updated so that they receive the correct order. Another benefit to real-time visibility into inventory levels is that you aren’t stocked to the hilt with slow-moving items or running out of items in demand. You can capture sales opportunities by ensuring there’s always enough, and revise your catalog accordingly.
-
Enhance Shipping Efficiency
The single biggest benefit to automated barcode scanning is that you can scan once to ensure mistakes don’t propagate to the final shipping stage. As a result, you can zoom through invoice and shipping label generation and improve sortation accuracy.
Even the footwork and congestion at warehouse zones come down when pickers know exactly where to go, which improves their picking efficiency and accuracy.
-
Improve Customer Experience
Getting the right order ahead of or on schedule makes you stand out in your customer’s mind, and increases their chances of returning and recommending your brand to others.
-
Prevent Inventory Shrinkages
Stolen, missing/unaccounted for items impact inventory levels between actuals and expected. Without barcodes, there’s no way to know when and where the issue originated. It helps you locate misplaced items or determine where it was last held, and who had it. These particulars curb inventory shrinkages by making movements visible and trackable.
Steps to Boost Fulfillment Accuracy with Base
The Base system gives a seller several options to activate barcode scans. It lets you customize the barcodes already available on the system specific to your business. To access it, go to
- The orders tab on the Base panel.
- Under settings, select keyboard shortcuts which lets you printout barcodes for use.
- Depending on the Automatic Actions a user takes, the barcode can launch by instruction.
- The instructions offered on the system are
- Opening an order on the order or return card.
- Activating the picking assistant to collect an order
- Activating the packing assistant to package the order.
- Clicking a picture
- Selecting or de-selecting a particular order’s status.
5. To enable the barcode, you can optionally go to Personal Events located under Automatic Action. The Settings box opens up to define the action and associated keyboard shortcut and color map. The last option is to check the box marked “enable barcode” before hitting save.
6. To print the barcode, go to the print summary.
7. Once the barcode is printed, the general settings of the barcode scanner is ready to activate.
8. Once the barcode is scanned, the user can open a card, select the orders from the list. You can either append items to an existing order against its barcode, or create a new order.
9. To add items to a specific order, the user will need to go to the EAN and scan it, which displays the products linked to it from the warehouse.
10. The barcode scanning system also alerts users as and when orders are received into inventory and helps regulate inventory control.
11. The barcode generated can activate the Picking Assistant and indicate the status of items that are yet to be picked. Similarly, it can also turn on the Packing Assistant to give the packing station a heads up as picked orders are routed.
12. The barcode capability applies to shipment code scans as well. The user can scan the label to open an order card.
13. From the list, select the orders and click on the Printouts/Exports section.
14. The user gets the Purchase Order in a PDF format and can print it out using the printout option.
Conclusion
A barcode scanning system plugged into your existing eCommerce suite can help you manage your orders, returns and inventory from a central location. Instead of visiting third party websites or apps to perform the scan and import the data manually, you can use the actions described in the steps discussed earlier above to save time and boost fulfillment accuracy.