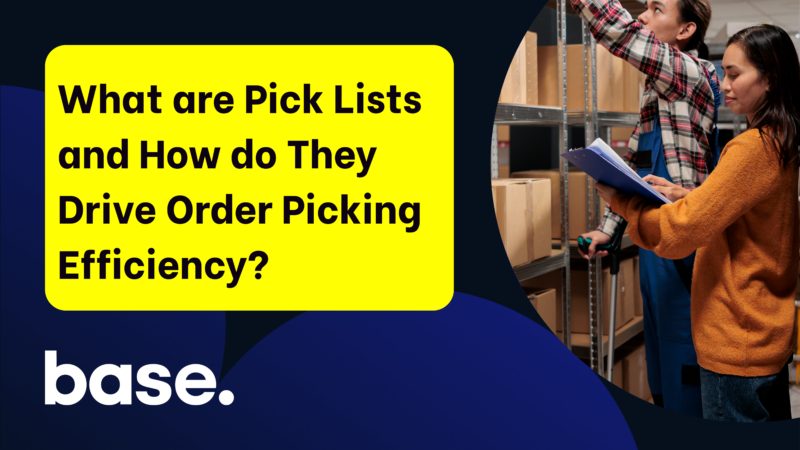
Order picking indicates the efficiency of the fulfillment process within your eCommerce business. And the supporting document that kicks order picking into high gear, is a pick list. Pick lists contain information on orders that enable the right products to move and get selected by the pickers and subsequently, packers.
Mistakes made in this stage propagate forward and lead to shipping delays and errors, with sellers sending customers the wrong products, paying excessive courier fees and using the wrong packaging material.
While it benefits sellers greatly to automate the picking process and thereby reduce paperwork, most sellers and warehouse operators work with paper in hand to confirm and close order processing. In light of why this makes sense, this article will cover what a pick list or picking list is and different ways to generate one that’s right for your business.
What Are Pick Lists?
A pick list is an all-inclusive document that is required by warehouse pickers for prompt and precise order fulfillment. It contains information on the items that they will need to fetch from inventory storage which includes SKU, quantity and exact location within the warehouse layout (i.e. shelf, bin or pigeon-hole). Order fulfillment commences once the pick list is generated. The more detailed and accurate the pick list, the easier and quicker it is for pickers to locate the specific items. And once the item is confirmed to match the order in terms of description, quantity, payment mode and shipping method, the remaining steps happen quickly, leading to on-time delivery.
Pick lists ensure search and walking time and the efforts associated with picking are reduced, preventing fulfillment SLA breaches. There are two types of picklists;
1. Physical pick lists
Paper pick lists are the old-fashioned way and involve the warehouse worker walking around with a paper printout, crossing off items as they select them. Despite mobile and Wifi, most smaller warehouses rely on physical pick lists.
On the Base system, there are 4 collection modes for picking which are;
- Collect as a group
- Collect one by one
- Collect in carts
- Collect with print (card and pen)
The Collect with print option has been recently introduced which offers warehouse workers a paper pick list digitized with a barcode. Packing stations can use this as well to confirm orders. It allows pickers to correctly collect goods using a dedicated printout.
How it works is that the system sends the pick list for printing automatically, which generates a barcode that appears on the printout. The pick list includes products that need to be collected and is grouped from all orders. The warehouse operator will walk around with this printout and mark items off as they are picked, bringing them back in a large basket. At the packing station where there are computer scanners, the packers can scan the barcode on the pick list and load up all orders that make up the pick list. This way, the picker can rely on paper without requiring a terminal while the packer can scan to confirm orders, determine packaging material and proceed to pack using the built-in packing assistant.
2. Digital pick lists
A Digital pick list features a barcode which can be scanned by mobiles or computer terminals on the warehouse floor. The order details are auto-assigned to pickers and all they have to do is follow the information on the handheld scanner to confirm and verify particulars such as the SKU, quantity, product images and accompanying description. This helps to validate that the picker is taking the correct item from the correct place.
Common Picking Methods
Given the direct link between fulfillment accuracy and customer satisfaction, the ultimate priority is to reduce the travel time and distance. From the effort perspective, order pickers tend to spend hours and cover significant distance (depending on the size of the warehouse). By making location information known, pickers know the shortest path to get to it which makes their job easier and moves things quicker. After all, this isn’t a single order or a one-off customer that we’re talking about but volumes with varying quantities, colors, sizes and other particulars. Having a pick list narrows this down and optimizes the pick-path, thereby raising operational efficiency. Picking methods vary depending on the warehouse layout, capacity, manpower and order volume, so here are a few commonly used methods;
-
Pick-to-order
Also known as Discrete picking or Picking By SKU, Pick to Order is most advantageous to small businesses handling fewer products because it essentially only requires you to hand your pickers a list and they go around the warehouse picking items to pack and ship. With fewer SKUs, this approach makes sense because you have the visibility needed to control the picking precision. However, it turns out to be an ineffective method in the long run if you decide to expand to a larger or few more warehouses which naturally means you’re moving to process higher order volume.
-
Batch picking
Batch picking works best for merging products for multiple orders into one picking instruction.
What this means, is that there can be 3 different product combinations as indicated below
Customer A | 4 toothbrushes, 2 tubes of toothpaste, 2 bar of soap |
Customer B | 2 toothbrushes and 3 dental flosses |
Customer C | 5 toothbrushes |
Rather than individually handling these orders, a worker will pick all quantities of toothbrushes for the customers combined and bring them to a dedicated sortation bay. The step is repeated similarly for the remaining items, creating batches. The workers then sort these according to the order and then send it for packing and shipping.
Batch picking makes sense for bundled orders because it requires workers to make fewer trips and pick more items which save time. All the items of a particular SKU will be in the same aisle so the time they spend there will be maximally utilized in terms of quantity. Picking on locations rather than orders helps you to position your best selling items in a particular section of the warehouse. Pickers know to go there only and will not waste time looking at the wrong places.
-
Zone picking
In zone picking, pick lists are either product or storage based and divide the warehouse into zones. Pickers are subsequently assigned to these zones,so they know exactly where they should be. Warehouses with very high-volume orders containing several products benefit from zone picking.
Zone picking also prevents lane congestion because pickers aren’t having to walk back and forth as much. They are confined to their zone and can concentrate on picking rather than walking.
-
Cluster Picking
Cluster picking is a picking method used to do numerous orders in one go. Instead of picking identical SKUS in bulk for several orders, pickers choose a wider range for each order.
Cluster picking is complemented with vertical lift shafts, conveyor belts and robotic assistant pickers. This minimizes errors and organizes the order fulfillment process a lot better. Agreed, you save more time with batch picking versus cluster picking, but the latter still ensures that the picker only has to visit a zone per cluster being processed.
-
Wave Picking
Wave picking has elements of batch and zone picking in it, where the orders are assigned in waves throughout the day, in warehouses split into zones. The pickers stay within their designated areas and perform their tasks simultaneously. The overall advantage to wave picking is that work occurs concurrently without dependencies, so it is best suited for companies whose orders feature various products.
Wave picking works best for companies using a dedicated warehouse management system because there are specific conditions to factor in, such as shipping time, transportation schedules and labor availability.
-
Pick-and-Pass Method
In this method, the warehouse is divided into different sections or zones, and each worker is responsible for picking items in a specific zone. As an order moves along, items are picked from one zone and then passed on to the next. Think of it as an assembly line in which every person adds their part before handing it off. This method is different from zone picking, where workers only pick items from their own area without passing along containers or bins.
-
Sorting System
Sorting systems cannot work without machines—like conveyor belts and sorting devices—to handle most of the sorting work. Pickers place items on a carousel, which carries them to the appropriate station for packing and shipping. It’s highly efficient because it reduces manual work and speeds up the entire order processing cycle.
-
Pick-to-Box Method
In the pick-to-box technique, boxes ride on a conveyor belt through the warehouse. As the box passes different zones, pickers add the required items directly into it. This method helps manage a high volume of orders and cuts down on picker congestion in busy areas.
-
Pick-to-Light
Pick to light is a paperless picking method that employs scanning devices to read information on products and help pickers to confirm they’re picking the right order. The LEDs are placed at racks and shelves throughout the warehouse. It usually works in the following manner;
- The system’s LED lights up, illuminating the path that the operator has to take to go to the right storage location. From there, the system informs the picker which items in what quantities should be picked.
- The worker picks the item and drops it into a holding container, and presses a button to confirm the picking.
- This continues until all items have been picked and placed into their respective containers or bins.
- Additionally, there are some systems that digitally read out options and instructions, and may ask the picker to report variations in pick size.
-
Picker-to-Part System
This system involves workers (often using forklifts or carts) moving around the warehouse to collect items for each order. It’s a practical method for organizing and assembling orders, especially when dealing with large or bulky products. Everything is picked from a designated area and brought together for shipment.
-
Part-to-Picker System
Also called the “goods-to-person” approach, this method brings the items to the picker instead of the other way around. Like the sorting system, it heavily relies on automation or robotics to move products from storage to the worker. Techniques like single-order picking, batch picking, and wave picking are used depending on how quickly orders need to be processed. It offers a flexible way to work, though it can involve longer movement times if not automated.
-
Piece Picking
In piece picking, warehouse workers pick one order at a time, choosing individual items for each customer. Since pickers aren’t multitasking across multiple orders, it reduces the chances of making mistakes. However, it can also cause the picker to expend more effort and prolong the process because the picker will need to walk around the warehouse several times for different orders. So it is best recommended for smaller businesses with fast moving daily orders.
-
Pallet Picking
Pallet picking involves picking entire pallets of goods. A pallet might contain one large item or many smaller ones. This method is ideal when a full pallet needs to be moved at once, such as when fulfilling bulk orders. It’s common in warehouses that handle large quantities of the same product.
-
Case Picking
In this method, workers pick entire cases or cartons of products instead of individual pieces. Depending on the product’s movement speed, items are picked from different types of storage:
- Fast-moving items: Picked from pallets for efficiency.
- Medium-speed items: Selected from carton flow racks.
- Slow-moving items: Retrieved from static shelves.
Pickers often use trolleys, conveyors, or pallet jacks to collect items as they go through warehouse aisles. This method offers a good balance between speed and flexibility.
Hybrid Picking Methods
If a single method doesn’t meet your warehouse needs, or you simply find yourself wanting to experiment with picking combinations, here are some hybrid order picking models to consider following;
Zone-Batch Picking
Here, pickers are assigned specific zones, and instead of handling one order at a time, they pick items for several orders in batches within their zone. This boosts efficiency without requiring them to travel beyond their designated area.
Zone-Wave Picking
This method involves assigning pickers to zones, and they must complete picking all items for all orders in that zone during a specific time window. It’s more structured and works well for timed operations.
Zone-Batch-Wave Picking
This is a layered strategy combining zone, batch, and wave picking. Each picker handles all items for multiple orders within their zone, and the work is scheduled in waves throughout their shift. It’s the most complex but also highly efficient for large-scale, time-sensitive operations.
Choosing an Order-Picking System
Now that you know that fulfillment accuracy and order picking efficiency are interlinked, running your business depends on the order-picking system you select. It not only delivers customers their orders undamaged and in the swiftest time possible but also utilizes existing warehouse space optimally.
We won’t suggest standardizing order picking because it should ideally evolve to businesses scaling up or ramping down operations. However, some key factors to consider prior to adopting a system are;
- The actual picking time or the time your pickers spend on picking.
- Worker safety
- Manpower capacity
- Products that you’re selling and the demand for them.
- Order size, frequency and volume, ie. how often do your customers order from you and in what quantities.
Given that travel time exceeds the actual picking time, it is important that the order picking method you use gets employees through the facility without endangering them. Rather than getting only 50% of the work done with repetitive back and forth, it’s about making every minute of their shift count by being in the right place at all times.
We recommend using a Pick-Pack AI integrated into an automated WMS software. It syncs offline scanning to online confirmation as orders are picked, expediting the pick-pack-ship process. Such a system practically pays for itself because you can
- Delight customers with prompt and precise deliveries.
- Provide workers with optimal routes and necessary verifications that reduce their efforts and increase their productivity.
- Reduce labor costs and time to generate documentation, such as a pick list, which ultimately helps pickers do their job more efficiently.
Try processing orders through the base system for the next 30 days to see what we mean!