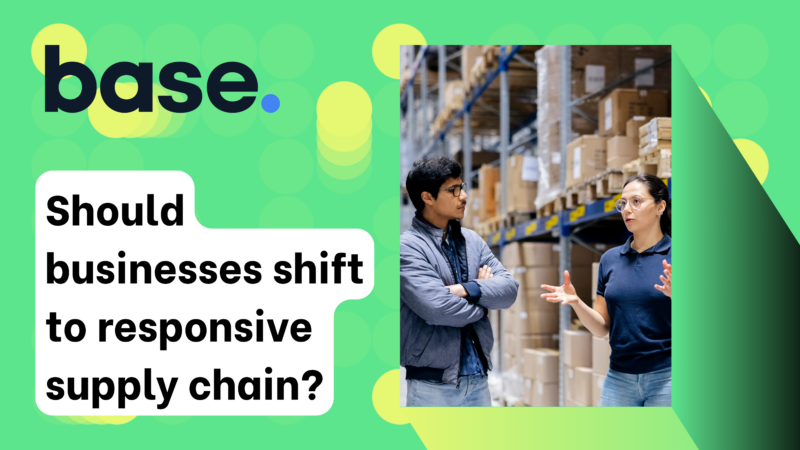
Sustainability is the watchword for supply chain resilience. The pandemic may have faded into the past, but it has forever changed the way supply chain executives view the trickle-down effect on customers. More businesses are considering shifting to responsive supply chains, favoring it over efficient supply chains to safeguard against the bullwhip effect. More than global events, it’s the smaller disruptions that have long term consequences because they are so deeply hidden within the supply network that their adverse effects remain undetected till they blow up.
Of course, responsiveness isn’t a one-size-fits-all definition. What one industry considers a responsive strategy needn’t necessarily work in another industry. A sustainable supply chain typically features both efficient and responsive strategies, but you’ll know when’s the right time to shift to it when efficiency is still disturbed.
In this quick read, we’re going to dive into tips for responsive supply chain management. Let’s start with;
What is a responsive supply chain?
A responsive supply chain anticipates uncertainty and lets businesses catch up to changing market conditions. It helps businesses explore alternatives and ramp up or down in response to abrupt demand shifts.
The suddenness with which a product’s popularity rises or declines leaves sellers with a tangible problem: inventory management. If there is a surplus that doesn’t sell fast enough or makes you money, you wind up paying more for storing it or discarding it when it spoils or expires. As a seller, you don’t fare better flipping the coin. Insufficient stock means you cannot capture opportunity, and it slips through your fingers.
With making the supply chain responsive, sellers can respond to either swings and stay afloat.
Efficient Vs Responsive: Learning to Tell the differences
While efficient and responsive supply chains both have common goals to meet and monitor- such as timely fulfillment, ship velocity, customer satisfaction and lead times, they are different in the following ways;
Efficient | Responsive |
consistency and cost efficiency | Agility and Continuity |
Designed for reliability | Designed for chaos |
Boosts performance by outsourcing parts such as fulfillment to a 3PL provider. | Keeps inventory flexible by maintaining a buffer inventory for unplanned demand. |
The importance of cultivating a responsive supply chain
A responsive supply chain helps merchants to
-
Expect and adapt to change
Fluctuations impact inventory and pricing which is why adaptability is the first place to start. Responsiveness makes it compulsory for sellers to check in on the competition, study trends and match it with their own sales history in order to understand the reasons and probabilities for seasonality.
A responsive supply chain doesn’t just optimize your inventory; it adjusts it to the demand such that you’re not overstocked on low-sales velocity items or running short on the moneymakers. It lets you launch new products before pressure for change builds up, and understand the market’s reception to it for you to make decisions concerning its continuity.
-
Risk response register
A responsive supply chain helps identify, classify and preempt risks with appropriate actions, such as changing suppliers, adjusting production timelines or procurement procedure.
For example, you have a best selling product that has shown a sharp decline in sales over the past 60 days. With a responsive supply chain, you can dig deeper, assess risk factors contributing to the decline and come up with a plan incorporating customer feedback. Rather than bank on future sales to be the same or higher only on the history, a risk analysis lets determine whether what you’re doing is worth continuing or needs further work. The risk is less when managed right!
3.Weed out Unsatisfactory Suppliers and Routes
At times, certain suppliers or routes may underperform or turn out to be unreliable in response to geopolitical conditions or mitigating circumstances. Continuing to depend on them, however, can undermine your attempt at consistent customer satisfaction, not to mention be detrimental to shipping SLAs. With a responsive supply chain, merchants can explore cost-effective transportation with suppliers and forge new supplier relationships.
4. Meet customer expectations
A responsive supply chain breaks siloes down and offers transparency through the chain. You can stay on top of several orders at once, drive sales and reinforce credibility just by remaining communicative. And the means to raise that bar is to make use of auto-response templates within a dedicated eCommerce platform.
Base, for instance, integrates with caller apps and Responso, a communication platform that lets you create sets of response templates to expedite customer reverts. Customer service teams making use of Responso can pull up tickets, determine context and automate appropriate responses that provide resolution or reassurance where required. Put simply, the response is swift and accurate.
5. Scale Quickly
A responsive supply chain helps you upscale and outgrow current capabilities with respect to order volume and sales. It keeps a buffer for unexpected demand surges such that you have enough inventory to go around across your warehouses and have time to ascertain how long this will spike in order to set up reorder points with suppliers.
The scaling likewise may have to ramp down , where you’ll need to adjust stock levels to waning interests and last-minute shopping indecision. Responsive supply chains help you stay in business during those leaner times by trimming your inventory.
Shifting to responsiveness from efficiency depends on the role it plays in helping you remain on-time, within costs and avoiding delays and penalties. In the next section, we’ll go into the how of weaving this into your supply chain.
5 tips to building responsive supply chains
Responsivity hinges on the level and type of incorporated technology that your business is ready to use for agility.
Step 1: Get unconditional supply chain visibility
Implement an automated inventory management system to track items as they move through different
Stages, from receiving to pick-to-ship. The visibility helps you to detect discrepancies and get to the bottom of unreconciled returns, unpaid dues, cycle count mismatches etc. With end-to-end visibility, your decisions are backed with facts that allow you to anticipate swings, forecast inventory, plan sales pipelines and optimize inventory levels accordingly.
Step 2: Cultivate trust in supplier relationships
Your suppliers contribute to your bread-and-butter, so treating them well allows communication to flourish. They can cut you good deals and provide goods even in the last-minute without overcharging you, helping you to avoid shortages. And these relationships can help you to widen your industry contacts by introducing you to trustworthy logistics and courier services that your supplier could have worked with in the past.
Step 3: Automate, Automate, Automate
Make use of automatic actions wherever you can which can reduce human efforts, errors and accelerate ship velocity. In the long run, automation saves you both time and money by narrowing search efforts, correct identification and sortation, pick-path optimization, raising POs, invoices, generating labels, responding to customer concerns and so much more.
The single biggest advantage of automation is that it’s highly customizable, allowing you to dictate the extent and use case most urgently needed for your business.
And in doing so, saving you the cost to use it.For example, you may find your staff spending more time on separating items according to marketplace orders. With a Pick-Pack AI Assistant as the one in Base, you can quickly check progress, modify existing orders by adding new items, or generate shipping labels for those prepaid orders that have been packed. You can even add as much information in product descriptions as you like in the language of your choice with an AI description writer.
With automatic actions you get to focus more on aspects critical to business success, such as product innovation and efficiency improvement.
Step 4: Provide organization-wide staff training
Your businesses’ ability to get the most out of any supply chain automation software depends on how ready and trained your staff are. Remember, operational efficiency is a reflection of staff competence, which is why software training is compulsory. Collect feedback from experienced staff on their problem areas for a comprehensive lesson plan that dives into resolution measures. As a next step, draft the training plan against their schedules to go over the aspects, business practices and compliance procedures in different areas of your business so that all knowledge is brought up to speed.
Step 5: Optimize regularly, tweak necessarily
Responsiveness should apply both to the supply chain as well as its improvement measures.
It is a process that merits regular reviewing. The starting point is data collection which allows you to assess the existing efficiency of warehouse operations, and analyze orders, sales growth, anticipated demand and unmet needs.
Additional filters can include region, location, customer details and courier service history. By improving the nerve center, i.e. the warehouse, resilience radiates outwards and streamlines inwarding and outwarding functions. The regular intervals for optimization helps you cut down shipping time, expedite picking both in time and accuracy, settle claims and pay the correct dues to your providers and stay tax-compliant.
To Be or Not to Be Responsive
This is a simple question to think about, but a tricky one to answer, because the supply chain is as responsive as the technologies powering it.
What helps to determine whether you should move fully onto a responsive supply chain, is to assess if your sales has outgrown your existing capabilities. Will your current technology stack and processes as well in the future as it’s in the present to help you upscale?
If you spend more time hiring manpower and they in turn deploy their manual efforts on running your warehouse, you know that efficiency is already compromised. The technology you use should allow you to weather volatility and take demand in stride rather than take spur-of-the-moment decisions that wind up costing you more in the long run.
Take a 30-day trial of the Base eCommerce automation engine to make your final decision the right one!